9 Proven Ways to Recycle Polyester Textiles: From Mechanical to Enzymatic
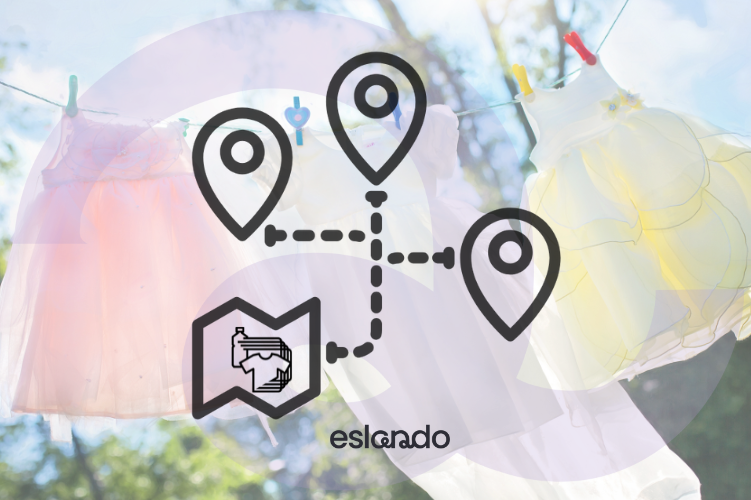
Have you ever wondered how many different ways there are to recycle polyester?
When most people think of recycling textiles — especially polyester — they usually imagine just two categories: mechanical and chemical. But that binary view is oversimplified.
In reality, there are several different pathways to recycle polyester, each with its own input requirements, processing technologies, and economic outcomes. A recent scientific review titled “Recycling processes of polyester-containing textile waste – A review” outlines this in detail.
And it confirms what we at Eslando have seen first-hand in the industry: polyester recycling is not one-size-fits-all. We believe that understanding these pathways — and matching the right waste to the right recycling process — is the only way forward for a circular textile economy.
Here is the summary of nine different methods for recycling polyester-containing textile waste:
1. Mechanical Recycling
Mechanical recycling is the process of breaking down textiles into individual fibres through tearing or garneting, with the goal of preserving fibre quality. These fibres can then be reused in non-woven products or spun into new yarns.
Pros:
- Low energy requirement
- Can handle mixed fabrics to some extent
- Suitable for post-consumer textile waste
Cons:
- Limited textile-to-textile applications
- Cannot remove dyes or mixed fibres
- Often results in downcycled output with lower mechanical properties
Use Cases: Often used for low-grade applications like filling, insulation, or automotive components.
Companies using the mechanical recycling method: Altex Non-Wovens (Germany)
2. Thermo-Mechanical Recycling
Combines thermal treatment and mechanical extrusion to recycle post-consumer textiles, especially polyester-rich blends.
Pros:
- Lower energy requirements than chemical recycling.
- Suitable for producing textile-to-textile fibres.
Cons:
- Requires clean and homogeneous input (mostly pure polyester)
- Still doesn’t chemically purify the polymer
- Performance depends heavily on input quality
Use cases: To date, thermo-mechanical recycling is mainly used for post-industrial textile waste or PET Flakes
Companies using thermo-mechanical recycling: Unifi (USA), Ganesha Ecosphere (India)
3. Glycolysis
Glycolysis is a chemical recycling process where PET waste is broken down using a chemical called ethylene glycol (EG). This process depolymerises (breaks down) the PET into its original building blocks, primarily a substance called bis(hydroxyethyl) terephthalate (BHET). These purified building blocks can then be used to create new, high-quality polyester, effectively creating a closed-loop recycling system. It’s a way to chemically rejuvenate polyester, making it suitable for new textile production.
Pros:
- Can deal with contaminated or dyed polyester waste
- Produces monomers that can be re-polymerised into virgin-quality PET
- Compatible with fibre-to-fibre recycling
Cons:
- Needs energy input
- By-product purification required
- Pre-treatment still needed in most cases
Use Cases: Glycolysis can break down dye-contaminated and additive-laden polyester fabrics into monomers.
Companies using glycolysis: Garbo (Italy), Jeplan (Japan)
4. Methanolysis
Methanolysis is the oldest chemical recycling technology. Uses methanol to depolymerise PET into DMT (dimethyl terephthalate) and ethylene glycol.
Pros:
- Produces high-purity monomers
- Good for removing additives, dyes, and blends
- Enables closed-loop recycling of PET fibres
Cons:
- High temperature and pressure are required
- Methanol is flammable and hazardous
- Large infrastructure and capital are needed
Use Case: Closed-loop recycling of coloured and contaminated polyester textiles into virgin-quality PET, suitable for use in textiles, packaging, and bottles.
Companies using methanolysis: Eastman (USA), Loop Industries (Canada)
5. Hydrolysis:
Hydrolysis, in polyester recycling, is a chemical process that uses water (often with acids or bases and heat) to break down PET into its original building blocks: terephthalic acid (TPA) and ethylene glycol (EG). These purified components can then be used to create new polyester.
Pros:
- Yields high-purity monomers
- Removes dyes, finishes, and contaminants
- Suitable for blended or coloured polyester waste
- Enables true closed-loop recycling
Cons:
- Requires corrosive chemicals and careful handling
- Generates wastewater that must be treated
- Energy-intensive process
- Costlier than mechanical recycling
- Still limited in commercial textile applications
Use Cases: Suitable for heavily dyed or contaminated polyester garments. Ideal when virgin-equivalent PET is the desired output
Companies using Hydrolysis: DePoly (Switzerland), Gr3n (Italy)
6. Enzymatic Hydrolysis
Uses engineered enzymes to break down PET into its building blocks at relatively mild conditions.
Pros:
- Low energy requirement
- High specificity, less degradation
- Environmentally friendly
Cons:
- Enzymes are expensive and sensitive
- Reaction times can be slow
- Still not widely commercialised
Use case: Low-energy, fibre-to-fibre recycling of PET textiles, especially suited for coloured or blended fabrics where conventional chemical methods are less effective.
Company using enzymatic hydrolysis: Carbios (France)
7. Pyrolysis and Gasification
Thermal decomposition of polyester waste at high temperatures (with or without oxygen) to produce gas, oil, or char at temperatures up to 520 °C.
Pros:
- Can handle mixed, contaminated textile waste
- Produces energy or chemical feedstocks
- No need for sorting
Cons:
- Not textile-to-textile
- Generates CO₂ and other emissions
- Low material circularity
Use cases: More common in chemical industries to generate pyrolysis oil than in fibre recovery.
Companies using pyrolysis and gasification: BASF, Pryme
8. Solvent-Based Recycling
Uses solvents to selectively dissolve and recover polyester, removing other components (like cotton or elastane).
Pros:
- Can separate blended fabrics
- Produces high-purity polyester
- Removes dyes and coatings
Cons:
- Solvent recovery required
- Risk of chemical exposure
- Expensive to scale
Use Case: Separation and recovery of polyester from multi-fibre blends (e.g. PET/cotton), enabling high-purity polyester extraction for reuse in textiles.
Companies using solvent-based recycling: WornAgain Technologies (UK)
9. Aminolysis & Ammonolysis
Breaks PET using amines or ammonia to yield terephthalamides or other amide compounds.
Pros:
- Potential for upcycling post-industrial textile waste into speciality chemicals
Cons:
- Produces products that cannot be polymerised to PET again.
- No possibility for textile-to-textile recycling.
- Not circular in the fibre-to-fibre sense
Current status: Still in early-stage research.
Why does choosing the right method matter? Our Final Thoughts
This review confirms something we experience every day at Eslando: polyester recycling isn’t just one process — it’s an ecosystem of technologies, each with its own needs, trade-offs, and economics.
For recyclers to succeed, they need the right type of waste at the right cost.
For suppliers to participate, they need clear incentives and guidance.
And for the industry to grow, we all need a platform that understands this complexity.
That’s why we built Eslando!
To match textile waste to the right recycling technologies — not just by material, but by condition, geography, contamination level, and more.
We believe data is the only way out of this complex nightmare, and collaboration is the only way forward.
Are you looking to source or trade polyester textile waste? Or right sourcing partners?
Join the Eslando Marketplace today: Signup here.
Watch out platform demo: https://youtu.be/nXzeuR5mEZM
Get in touch with us us on info@eslando.com